Aluminum alloy materials are known for their light weight, high strength, good rigidity, corrosion resistance, heat dissipation, impact resistance, anti-electromagnetic interference and shielding properties, excellent processing performance and lower processing costs, and excellent recycling performance (recycling and regeneration High efficiency, low regeneration cost), etc., are being favored by more and more industries, and become a new star of materials.
After the aluminum alloy parts are produced by casting, they generally need to undergo subsequent CNC processing and surface treatment before they finally become finished parts and are applied to related products. Usually, during the CNC processing of aluminum alloy parts, it is often found that there are large areas of black spots on the surface of many products, which are not easy to be polished off, seriously affecting the appearance of the product, and causing the product to be scrapped.
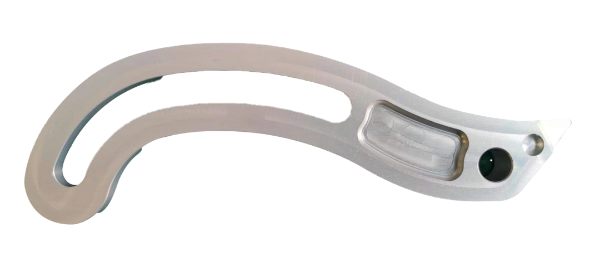
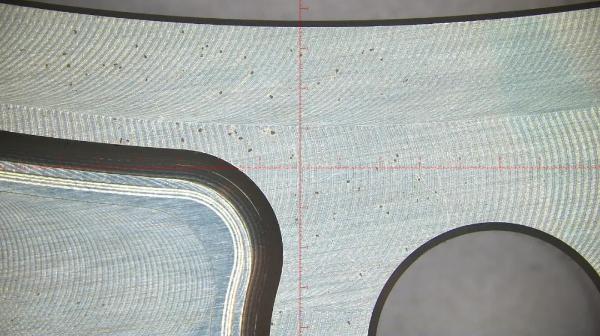
Distinctive black spots randomly distributed on the surface of the part can be seen.
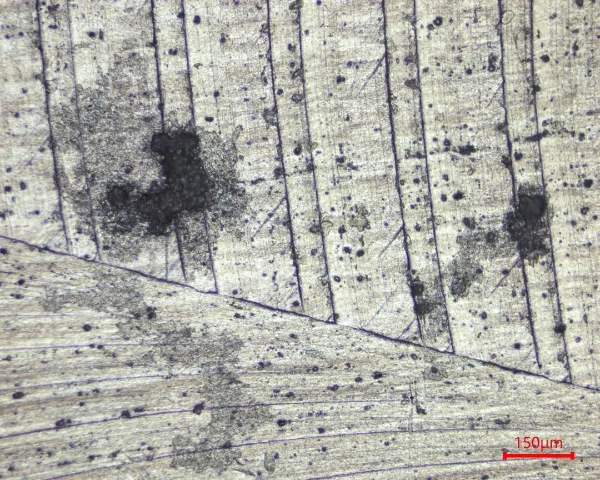
Point defect 100×
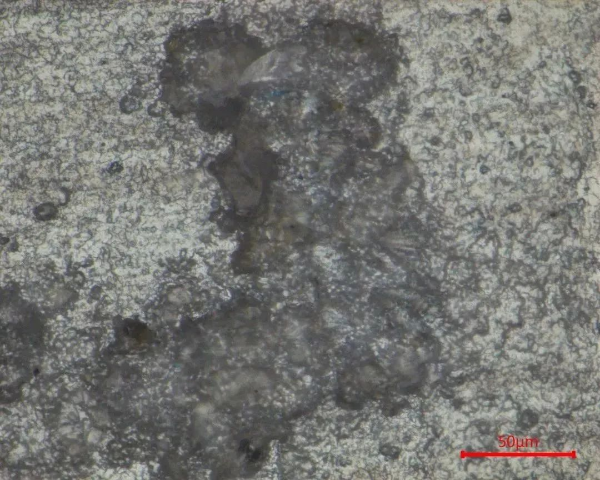
Point defect 500×
When the defect is enlarged and observed, it can be seen that it is a pit, the bottom of the pit is arc-shaped, and there are filamentous corrosion lines around the pit. At the same time, the boundary lines of aluminum alloy grains can be vaguely seen.
01 Cutting
Use TableCUT-200 manual precision cutting machine to cut the sample.
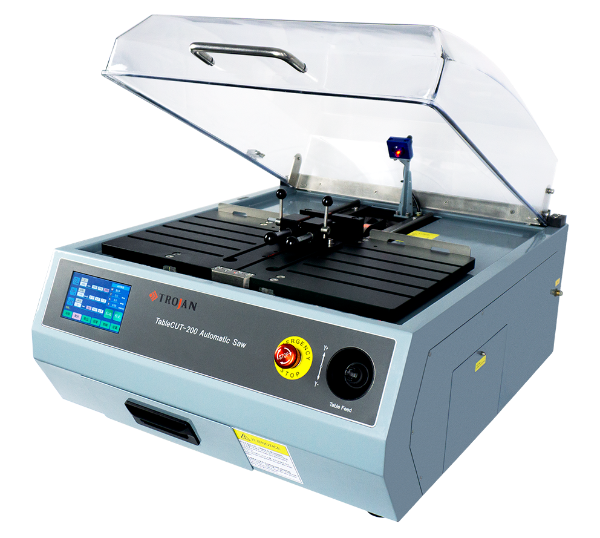
TableCUT-200 Automatic precision cut-off machine
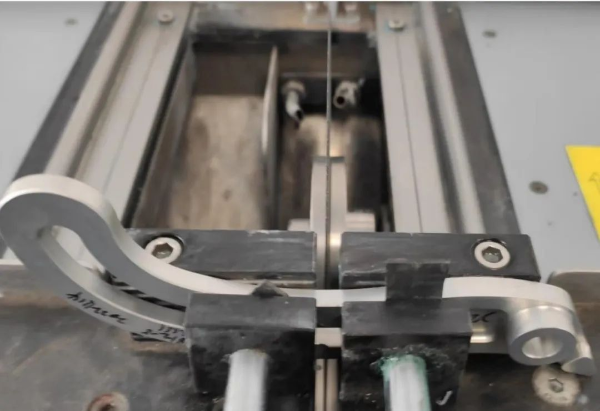
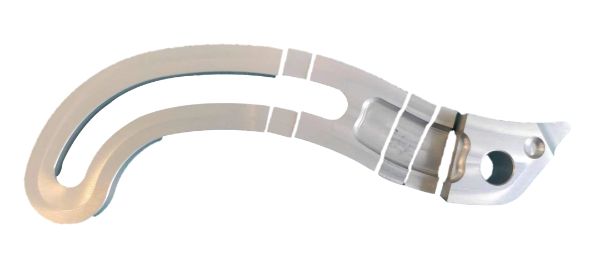
Equipment |
TableCUT-200 Automatic precision cut-off machine |
Consumables |
SiC cutting blade |
Parameter |
0.2mm/s,3000rpm |
02 Mounting
The samples were mounted using the Trojan FlexPRESS Mounting Press, and the thermal mounting material was TJ2231.
FlexPRESS Fully automatic hot mounting machine
Equipment |
FlexPRESS fully automatic hot mounting machine |
Consumables |
TJ2231 |
Parameter |
180℃,180bar,5min,moderate cooling |
03 Grinding
Use Alpha-600 automatic grinding and polishing machine to grind the sample, abrasive paper P400→P2500.
Alpha-600 Automatic Grinder&Polisher
Trojan metallographic abrasive paper
Equipment |
Alpha-600 automatic grinder&polisher |
Consumables |
Abrasive paper:P400;P800;P1200;P2000;P2500 |
Parameter |
Pressure:18N,upper speed: 80rpm,lower speed:120rpm,time: 2min |
04 Rough polishing
Use Alpha-600 automatic grinding and polishing machine to polish the sample, use YS polishing cloth with 3μm polycrystalline diamond polishing fluid for rough polishing while adding polishing lubricant.
Alpha-600 automatic grinding and polishing machine
YS-JP white fiber polishing cloth
PD-W polycrystalline diamond suspension
Equipment |
Alpha-600 automatic grinder&polisher |
Consumables |
YS polishing cloth,3μm polycrystalline diamond suspension, polishing lubricant |
Parameter |
Pressure 20N,Upper speed80rpm,lower speed 150rpm,time: 5min |
05 Fine polishing
Use Alpha-600 automatic grinding and polishing machine to polish the sample, and then use ET polishing cloth for fine polishing with 0.05 μm silica polishing fluid.
Alpha-600 automatic grinding and polishing machine
ET-JP White synthetic velvet polishing cloth
SO T401 colloidal silica polishing liquid
Equipment |
Alpha-600 automatic grinding and polishing machine |
Consumables |
ET polishing cloth,0.05μm colloidal silica polishing liquid |
Parameter |
Pressure:15N,upper speed: 80rpm,lower speed:120rpm,time:3min |
06 Observation
Equipment |
OUMIT MT60 metallographic microscope |
Parameter |
50×→500× observation |
07 Analysis
surface dimples 500×
surface dimples 500×
surface dimples 500×
surface dimples 1000×
①:square test block 200×
②:I-shaped test block 200×
From the cross-sectional view of the pits, it can be seen that the bottom is relatively round and smooth, and some pits are honeycomb-shaped, which conforms to the characteristics of pitting corrosion.
The grain elongation and deformation of the I-shaped sample are obvious, and there is a large deformation energy storage inside, and the electrode potential difference that causes corrosion is large, so more pitting corrosion occurs there.
On the surface to be cut, the primary intermetallic compounds Al7FeCr, Al3Fe, Mg2Si, etc. are exposed on the surface of the part by cutting. Compared with the α-Al matrix, it has a higher electrode potential and forms a corrosion cell centered on the primary phase in the cutting fluid. Causes extremely rapid pitting corrosion.