The polishing methods of metallographic samples are divided into mechanical polishing, electrolytic polishing and chemical polishing according to their function essence.
The principle of metallographic grinding and mechanical polishing
Mechanical polishing is the result of the relative action of the polishing powder and the grinding surface of the metallographic sample. Polishing powder is finer than polishing abrasives. It is generally believed that the effect of polishing abrasives on the surface of the sample during the polishing process has two aspects.
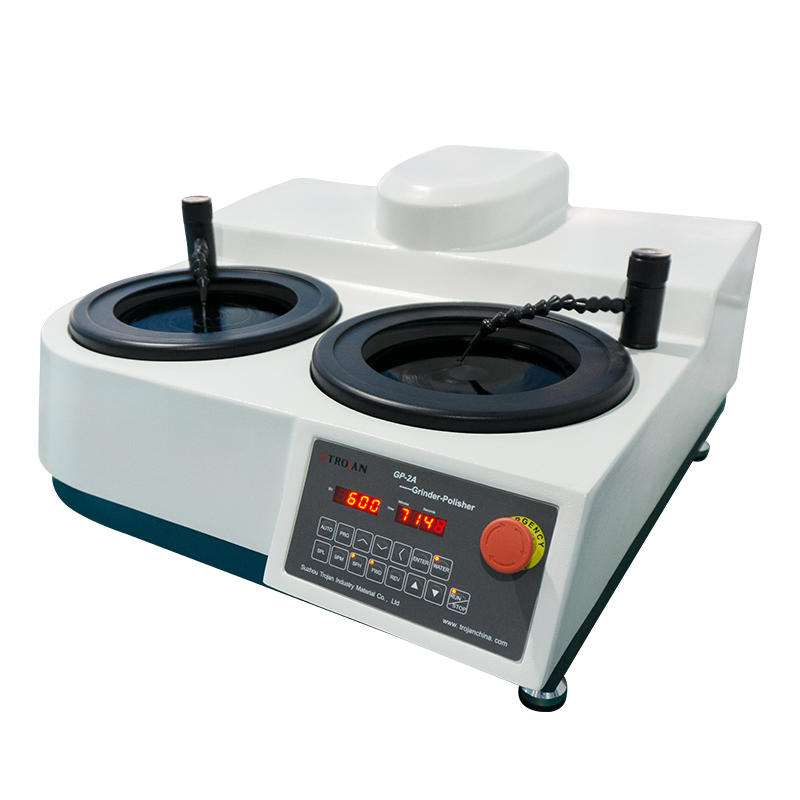
(1) Grinding function of metallographic grinding and polishing machine
The polishing particles are embedded in the gaps of the polishing fabric to obtain temporary fixation, which acts like sandpaper for polishing, but the cutting and scratching on the surface of the sample is much finer than that in polishing.
(2) Rolling action of metallographic grinding and polishing machine
Polishing particles are easily detached from the polishing fabric and even fly out of the polishing disc. These protruding particles are sandwiched between the polishing fabric and the grinding surface of the sample during the polishing process, which produces a mechanical rolling effect on the grinding surface, so that the protruding parts of the metal surface migrate to the concave parts. In addition, the mechanical friction between the polishing fabric and the abrasive surface also contributes to the "flow of metal".
Obviously, the rolling action of the polishing process will produce a thin deformation layer, the so-called Bayer layer, or the disturbance layer, so that the polishing surface cannot correctly display the original structure, which is not desirable. The process parameters should be chosen to minimize the thickness of the Bierper layer.