1. Coarse grinding
Rough grinding means smoothing, which is to trim and shape the rough surface formed by sampling and the sample whose shape is filled, and trim it to be flat according to the inspection purpose and the direction of the grinding surface (longitudinal and transverse). Coarse grinding can be done manually or mechanically. Manual operation is used for softer non-ferrous metals and their alloys. Generally, coarse sandpaper is used to trim the shape and surface, but not a grinder, because soft metals easily fill the gaps of the grinding wheel, dull the grinding wheel, and deform the surface of the sample. layer thicker. Mechanical operation is suitable for harder steel materials and can be dressed on a grinder, belt grinder or grinder. The grinder should use a special grinding wheel and cannot be used for grinding other tools, otherwise the side of the grinding wheel will be uneven, and the grinding surface of the sample after rough grinding will not be smooth. Generally, the shape is trimmed on the circumference of the grinding wheel, and the grinding surface is trimmed on the side of the grinding wheel.
Note: When using the rough mold of the grinder, care must be taken that the contact pressure is not too large, and the sample needs to be cooled to prevent the sample from being heated and causing tissue changes
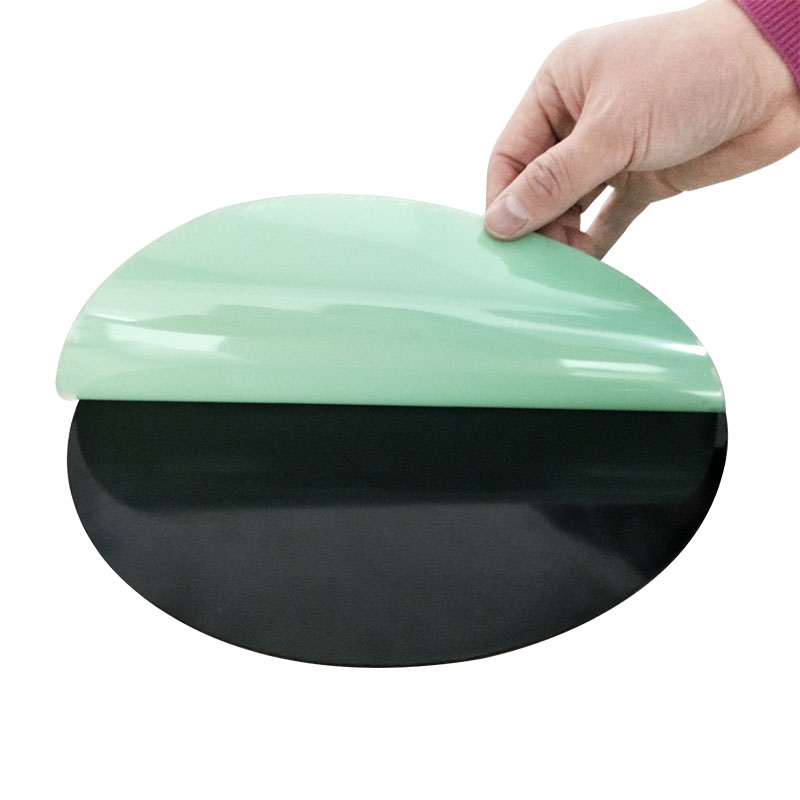
2. Fine grinding
Fine grinding is polishing, mainly to eliminate the metal damage layer on the surface of the sample.
When fine grinding by hand, it is carried out on metallographic sandpaper of various sizes from coarse to fine. Commonly used metallographic sandpaper grades are: 240#, 400#, 600#, 800#, 1000#, etc. Lay the sandpaper flat on the glass plate, metal plate, plastic plate or wooden board, press the sandpaper firmly with one hand, hold the sample steadily with the other hand, press the abrasive surface lightly on the sandpaper and push it forward, then lift and pull it back. The specimen should not come into contact with the sandpaper while pulling back. Do not grind back and forth, otherwise the grinding surface is easy to form an arc, and a flat grinding surface cannot be obtained.
Attention should be paid to manual fine grinding: every time you replace the No. 1 sandpaper, you need to wash the sample and your hands, and turn 90° to grind vertically with the old wear marks. The purpose of the rotation is to see whether the previous wear marks are completely removed, and after It is beneficial to remove the deformation layer produced by the previous sandpaper grinding, so that the grinding surface remains flat. The amount of pressure applied during polishing should be appropriate. The force should not be too large and the time should not be too long, so as to avoid the oxidation of the surface of the sample to generate a new damage layer, which will bring difficulties to polishing. The polished sample is observed under a metallographic microscope, that is, it shows fine traces in one direction.
In addition to manual fine grinding, mechanical grinding can be performed with a metallographic sample grinding and polishing machine. However, pay attention to water cooling during the process to avoid overheating of the grinding surface.