Metallographic grinding and polishing machines are essential tools for preparing materials for examination under a microscope. These machines use abrasive discs or belts to grind and polish samples to a smooth and flat surface. In this article, we will provide a comprehensive guide to metallographic grinding and polishing machines.
There are several types of metallographic grinding and polishing machines available in the market. The most common types are:
Single disc machines: These machines have one abrasive disc or polishing cloth and are suitable for small and simple samples.
Dual disc machines: These machines have two abrasive discs or polishing cloths and are suitable for larger and more complex samples.
Automatic machines: These machines are fully automated and can perform all grinding and polishing steps automatically.
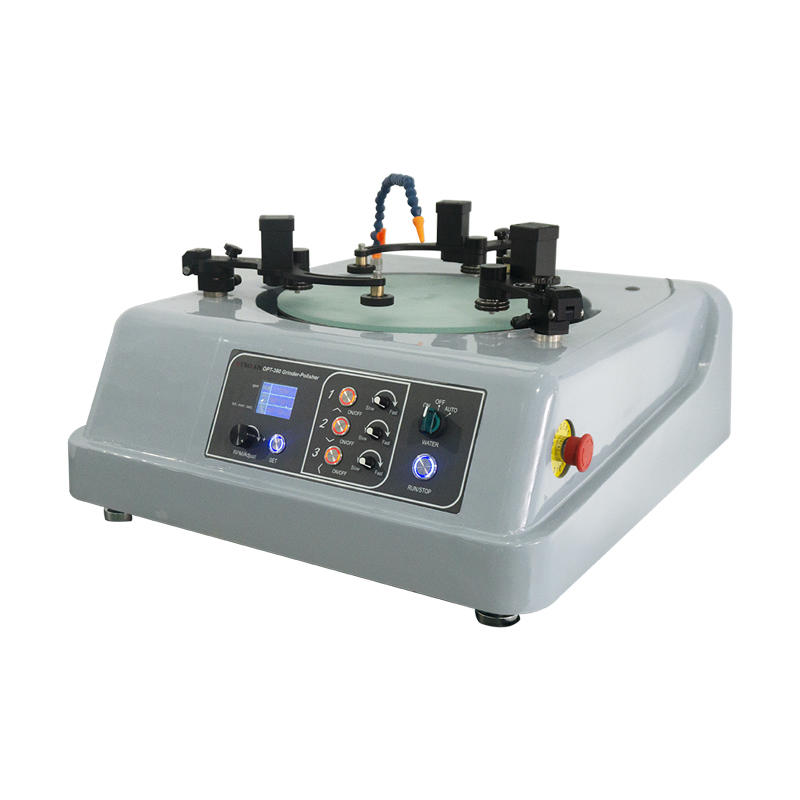
Manual machines: These machines require manual operation and are suitable for small-scale use.
Features of Metallographic Grinding and Polishing Machines
Metallographic grinding and polishing machines have several features that make them effective for preparing samples. These features include:
Adjustable speed: Machines can adjust their speed to suit the type of material being prepared.
Water cooling system: Machines can have a water cooling system to prevent samples from overheating during the preparation process.
Automatic head pressure: Some machines have an automatic head pressure system that can adjust the pressure applied to the sample automatically.
Digital display: Some machines have a digital display that shows the speed, pressure, and other settings.
The Grinding and Polishing Process
The grinding and polishing process is a crucial step in preparing samples for examination under a microscope. The process involves the following steps:
Grinding: The first step is grinding the sample with an abrasive disc or belt to remove any surface irregularities.
Polishing: The second step is polishing the sample with a polishing cloth to achieve a smooth and flat surface.
Etching: The third step is etching the sample with a chemical solution to reveal the microstructure of the material.
Examination: The final step is examining the sample under a microscope to analyze its microstructure and identify any defects or anomalies.
Applications of Metallographic Grinding and Polishing Machines
Metallographic grinding and polishing machines are used in a variety of industries, including:
Materials science: Researchers use metallographic grinding and polishing machines to prepare samples for examination and analysis.
Manufacturing: Metallographic grinding and polishing machines are used to prepare samples of manufactured products for quality control purposes.
Forensics: Metallographic grinding and polishing machines are used in forensic analysis to examine materials related to criminal investigations.
Metallographic grinding and polishing machines are essential tools for preparing samples for examination under a microscope. By choosing the right type of machine with suitable features, researchers and manufacturers can prepare high-quality samples with ease. With their applications in materials science, manufacturing, and forensics, metallographic grinding and polishing machines play a vital role in many industries.